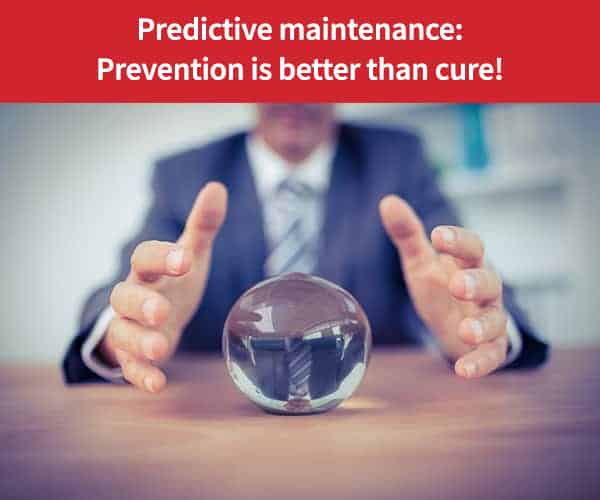
- Analytics
- Internet of Things
- Maintenance
- Technologies
Predictive maintenance: Prevention is better than cure!
The saying “prevention is better than cure” is very relevant to maintenance activities. In today’s era of big data, Industry 4.0 and the Internet of Things (IoT), new technologies are enabling field service companies to evolve from corrective maintenance strategies to predictive strategies.
A June 2017 study conducted by the Aberdeen Group Research Institute shows that 37% of service companies plan to use predictive analytics tools to enhance their maintenance strategies.
In this article, we will introduce you to predictive maintenance and tell you a bit about the benefits it can bring to your business.
Corrective, preventive and predictive maintenance
Let’s start with a few definitions.
Corrective maintenance, which is also called curative maintenance, makes sure that equipment is repaired after a failure has occurred. Failures are not predicted or anticipated. Instead, technicians intervene to correct the problem after the breakdown.
Preventive maintenance makes sure that equipment receives regularly scheduled service to help keep it running smoothly. Because maintenance activities are scheduled based on the expected lifecycle for equipment, preventive maintenance can help to anticipate and avoid potential failures.
The timing of problem detection is the main drawback with preventive maintenance. If wear or a defect is detected on a part in fully functioning equipment, that part is replaced as a precaution in case it could lead to a failure down the road. This approach often results in unexpected expenses that customers could have avoided or postponed.
Predictive maintenance “helps determine the condition of in-service equipment in order to predict when maintenance should be performed. This approach promises cost savings over routine or time-based preventive maintenance because tasks are performed only when warranted,” according to the Wikipedia definition.
Predictive maintenance pushes maintenance tasks a step further than preventive maintenance.
To predict when maintenance is required, intelligent sensors are added to equipment so they can transmit data about equipment operation. By analyzing the data sent by the sensors, field service companies can adopt a “just in time” approach, repairing or replacing equipment just before a failure occurs to optimize the amount of time equipment can be used.
Predictive maintenance forecasts technical issues instead of allowing them to occur. With a predictive maintenance strategy, field service companies can schedule service calls in advance to avoid unexpected stoppages in equipment operation.
Setting up a predictive maintenance strategy
The first step in establishing a predictive maintenance strategy is to install sensors on the equipment. The sensors allow you to collect data about the equipment’s operational state. You can then use software to analyze the data according to specific parameters. This lets you establish what normal behavior looks like and set the thresholds at which imminent failure warnings are generated.
Smart sensors
A number of different types of industrial sensors are available. Many types of modern equipment come with smart sensors already installed. Here are just a few of the many types of sensors used today:
- Ultrasonic flaw detection
- Infrared thermographic analysis
- Vibration analysis
- Fluid analysis
- Oil analysis
- Spectral analysis
Artificial intelligence and predictions
Analytics tools help you reveal the insight that is hidden in the data collected by sensors so you know where maintenance is required. This is the world of artificial intelligence (AI). AI algorithms can find and analyze the data that is characteristic of an imminent breakdown. From there, the algorithms model similar data combinations and failure scenarios and set warning thresholds accordingly. When one of the combinations reappears, a failure is considered to be imminent.
When field service management software, such as the solution offered by Praxedo, is connected to the analytics software, you can automate decisions about which maintenance activities must be scheduled and in what timeframe.
Integration of information systems
Integrating all of the different information systems involved is critical to the success of a predictive maintenance strategy. Maintenance data must be centralized so it can be accessed by the analytics software. Cloud technologies enable this data centralization. The Aberdeen Group study indicates that companies using predictive analytics technologies to enable maintenance strategies are 33% more efficient in creating a unified view of their data from all of their information systems.
Predictive maintenance costs and benefits
Implementing a predictive maintenance strategy provides significant savings over corrective and preventive maintenance because tasks are only performed at the appropriate time. You can anticipate exactly when a failure will occur and intervene only when the need is clearly established. Timing, cost, and operational tradeoffs are balanced: costs are reduced because service is not provided before it is needed, and complete breakdowns are avoided because service is provided just in time.
Initial investments are needed…
Implementing a predictive maintenance strategy can be a significant cost to your business. You’ll need the sensors necessary to ensure continuous equipment monitoring as well as analytics software to extract insight from the sensor data. You also need to consider the cost of training your teams to take full advantage of these new data analysis tools. Then, you need to plan the time to develop and deploy the program….
To enable significant operational benefits
In return for the time and money you put into your predictive maintenance program, there are enormous benefits, especially over the long term:
-
A significant reduction in equipment breakdowns and downtime
-
Better equipment monitoring so you can anticipate minor incidents that could lead to larger problems
-
Optimal use of equipment (until the moment before failure) and a longer life expectancy
-
Higher equipment reliability to optimize production
-
Better ability to plan maintenance activities and prepare maintenance teams for the required tasks
-
Better spare parts management
-
Lower maintenance and downtime costs for equipment
As an example, in 2014 the consulting firm, Roland Berger, produced a study indicating that energy companies that implemented predictive maintenance programs successfully eliminated up to 75% of equipment failures.
This proof point perfectly captures the concrete advantages of setting up a predictive maintenance program, particularly in the industrial sector, where maintenance-related interruptions in production facilities can very quickly become very expensive.
So, when will you switch to predictive maintenance?
Our similar articles.
-
- Maintenance
- Technician
- Optmisation
The key to unlocking a super-responsive automatic door aftermarket service offering
May 13, 2021 -
- Technologies
- Software
- Customer Satisfaction
- SAV
- Logiciel
- Software
Balancing humans and technology in aftermarket service
March 10, 2021 -
- Maintenance
- Technician
- Security
- Technicien
- Work orders
- Mobile app
Ensuring the safety of maintenance technicians
November 25, 2020